ANALISI METALLURGICHE
Prove meccaniche
In molte applicazioni industriali, le proprietà fisiche dei materiali sono cruciali per la longevità di prodotti e strutture. Il modo migliore per determinarne la resistenza alla deformazione ed il comportamento è sottoporli a sollecitazioni esterne fino ad arrivare, in alcuni casi, a rottura del materiale. I test distruttivi meccanici spesso forniscono più informazioni e sono più facili da interpretare rispetto ai test non distruttivi.
Il nostro laboratorio esegue una vasta gamma di test distruttivi meccanici come prove di trazione, prove di flessione, prove di impatto e prove di durezza secondo le più diffuse norme ISO e ASTM. La nostra officina meccanica interna prepara i campioni per tutti i test meccanici, il che rende possibili tempi di consegna brevi
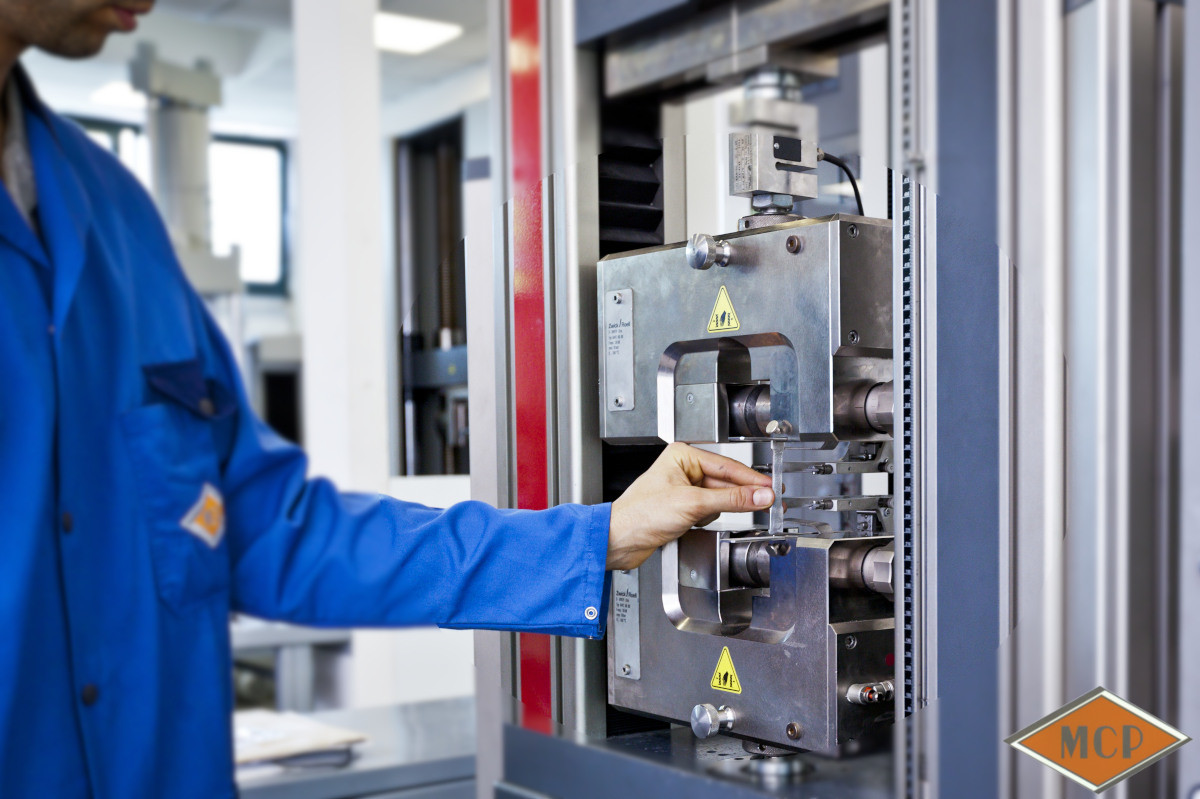
Prove meccaniche eseguite dal nostro laboratorio
- Resistenza alla trazione / test di snervamento a caldo
- Prova di impatto (Charpy)
- Prova di flessione
- Prova di rugosità
- Prova di durezza (Rockwell, Brinell, micro Vickers)
- Prova di trazione dell’anello
- Prova di espansione dell’anello
- Prova di appiattimento
- Prova di svasatura
Prova di trazione
Le prove di trazione, fondamentali per verificare la conformità meccanica dei materiali metallici, vengono eseguite secondo gli standard internazionali UNI EN ISO 6892-1 (Materiali metallici – Prova di trazione – Parte 1: Metodo di prova a temperatura ambiente) e ASTM A370 (Standard Test Methods and Definitions for Mechanical Testing of Steel Products).
La prova di trazione consiste nel sottoporre una provetta di dimensioni standardizzate ad una forza di trazione crescente fino alla rottura. Durante la prova di trazione, la provetta si allunga proporzionalmente alla forza applicata fino al limite elastico del materiale, oltre il quale la provetta si deforma progressivamente e in maniera permanente (deformazione plastica).
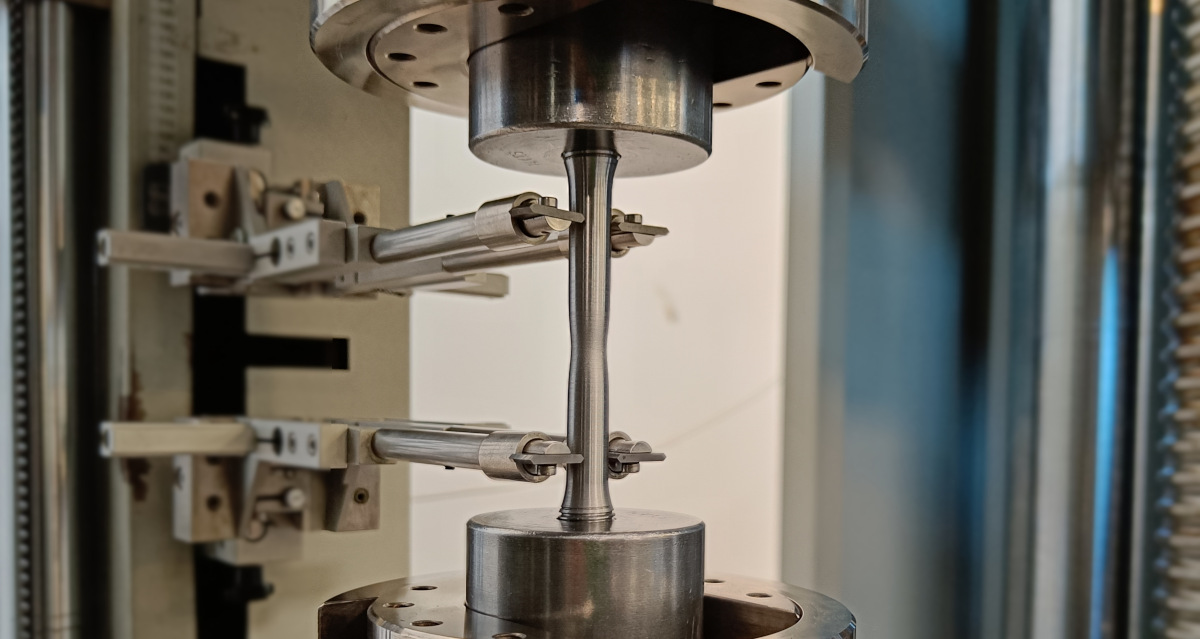
Proseguendo la prova, la forza applicata raggiunge il suo valore massimo, inizia la strizione della provetta che subito dopo si rompe proprio nella zona di strizione. Normalmente eseguiamo la prova di trazione a temperatura ambiente (10÷35°C) in base alla UNI EN ISO 6892-1:2020 (o in alternativa ASTM E8/E8M), ma siamo in grado di eseguire anche la prova a temperatura elevata (fino a 1100°C) secondo la UNI EN ISO 6892-2:2018 (o in alternativa ASTM E21) su provette di forma cilindrica e teste di serraggio filettate.
Le caratteristiche fondamentali che forniamo sempre al cliente nel resoconto della prova di trazione sono:
- Resistenza a trazione o carico massimo unitario Rm in MPa
- Il carico unitario di snervamento superiore (ReH o ReL) oppure il carico unitario di scostamento dalla proporzionalità (Rp0,2) in MPa
- Allungamento a rottura percentuale (A%)
- Strizione (Z%)
Se richiesto specificamente dalla norma di prodotto o dal cliente, possiamo indicare anche le seguenti grandezze:
- Modulo di elasticità o modulo elastico a trazione (E) in MPa
- Carico unitario limite d’allungamento totale Rt in Mpa
- Carico unitario d’allungamento permanente Rr in Mpa
- Allungamento percentuale totale dopo rottura At
- Allungamento percentuale totale sotto carico massimo Agt
Per la valutazione precisa di queste grandezze, tutte le macchine di trazione del laboratorio sono dotate di dispositivi automatici (estensimetri elettronici) che applichiamo alla provetta fino alla fine della prova e che si interfacciano costantemente con la macchina di prova computerizzata. L’utilizzo dell’estensimetro elettronico per tutte le provette di qualunque forma e dimensione, ci consente di evitare di praticare pericolosi intagli sulla provetta per marcare le estremità della lunghezza iniziale tra i riferimenti, intagli che potrebbero favorire la rottura falsando i risultati.
Prova di resilienza
La prova di resilienza misura l’energia necessaria per rompere mediante urto una provetta di forma e dimensioni standardizzate. In particolare, il coltello della mazza del pendolo colpisce la faccia senza intaglio della provetta sistemata sugli appoggi del pendolo. L’energia d’urto assorbita dalla provetta viene assunta come misura della tenacità del materiale (solitamente acciaio) con cui la provetta è realizzata.
MACCHINA DI PROVA
La macchina utilizzata in Modena Centro Prove è un pendolo di Charpy che sviluppa un’energia d’urto di 750 J ed è conforme alle norme UNI EN ISO 148-2:2016 e ASTM E23. Il valore della resilienza viene letto direttamente sulla scala graduata e sul display digitale dell’encoder, che misura la differenza fra l’altezza di caduta e l’altezza a cui risale il pendolo dopo la rottura della provetta.
TIPI DI PROVETTE DI RESILIENZA
Le provette che utilizziamo per le prove di resilienza sono di due tipi: la Charpy con intaglio a V e la Charpy con intaglio a U normale. Poiché l’intaglio viene realizzato dalla nostra officina mediante una fresa specifica, siamo comunque in grado di realizzare anche altri tipi di intagli tra quelli proposti nelle norme unificate. Per materiali molto fragili, possiamo eseguire la prova anche su provette senza intaglio che si rompono ad energie d’urto modeste. La prova di resilienza viene sempre eseguita su 3 provette ed è il valore medio dei risultati delle tre prove che deve soddisfare le prescrizioni.
TEMPERATURA DI PROVA
Eseguiamo prove di resilienza sia a temperatura ambiente (23±5°C) che a temperatura inferiore a quella ambiente fino a -96°C. Quando la temperatura di prova è diversa da quella ambiente, le provette vengono immerse in un liquido refrigerante (etanolo) contenuto in un criostato controllato elettronicamente in grado di mantenere la temperatura del bagno con una precisione di ±1°C e garantire l’uniformità della temperatura.
Prova di durezza
È la prova più diffusa nell’industria meccanica, soprattutto per il trattamento termico, per l’immediatezza dell’informazione e la relativa semplicità del controllo. Le prove di durezza sono generalmente facili da eseguire, non danneggiano irreversibilmente i pezzi provati se eseguite correttamente e consentono di valutare rapidamente le caratteristiche meccaniche del materiale senza ricorrere a prove più complesse e distruttive come la prova di trazione. Per i metalli, le prove eseguite dal nostro laboratorio sono:
- le prove Brinell (HB) secondo UNI EN ISO 6506-1:2015
- le prove Vickers (HV) secondo UNI EN ISO 6507-1:2018
- le prove Rockwell (HRC) secondo UNI EN ISO 6508-1:2016
PROVA DI DUREZZA BRINELL (HB)
Per la prova viene utilizzata una sfera in metallo duro (carburo di tungsteno) appoggiata sulla superficie del campione, alla quale viene applicato il carico di prova che la fa penetrare nel campione lasciando un’impronta circolare il cui diametro viene misurato mediante sistemi ottici automatici o manuali. Tramite una formula riportata nella norma di riferimento UNI EN 6506-1:2015 è possibile risalire al valore della durezza Brinell. La norma consente l’utilizzo della sola sfera di metallo duro come penetratore per cui il simbolo della prova di durezza è semplicemente HB (Hardness Brinell): non è più ammessa la prova con sfera d’acciaio HBS (Hardness Brinell Steel). Il diametro della sfera può essere 1, 2,5, 5 e 10 mm e per tutte le sfere sono ammessi solo i seguenti rapporti tra Ø sfera e carico applicato: 30, 10, 5, 2,5 e 1. Le varie combinazioni Ø sfera/carico sono prescritte dalla norma di riferimento e dalla norma di prodotto ma dipendono anche dalle caratteristiche meccaniche e dalle dimensioni del campione di prova. Quest’ultimo deve essere accuratamente preparato in modo da ottenere una superficie di prova liscia e perfettamente planare: durante la spianatura occorre evitare il surriscaldamento o l’incrudimento della superficie della provetta per non alterare la durezza dello strato superficiale con possibili errori di misura. Il valore della durezza Brinell si ottiene misurando il diametro dell’impronta lasciata dal penetratore: è quindi indispensabile che lo strumento di misura sia dotato di un sistema di lettura molto preciso: tutti i durometri del nostro laboratorio utilizzano solo obiettivi che offrono la massima risoluzione ottica e software di misura completamente automatici che valutano automaticamente il diametro dell’impronta per la massima affidabilità della misura.
PROVA DI DUREZZA VICKERS (HV)
La prova utilizza un penetratore di diamante, a forma piramidale retta con base quadrata, al quale viene applicato un carico che lo fa penetrare nel campione lasciando un’prevede impronta a forma di rombo che viene poi accuratamente misurata. E’ fondamentale che la superficie del campione da testare sia perfettamente liscia in modo da leggere le diagonali dell’impronta con sufficiente precisione, per cui in genere la preparazione del campione è più laboriosa rispetto a quella per la misura Brinell. La norma UNI EN ISO 6507-1:2018 prevede numerosi carichi di prova a partire da 10 gf (HV0,01) per le misure di microdurezza, fino a 100 Kgf (HV100) per le prove normali. La misura delle due diagonali dell’impronta è eseguita mediante oculari con opportuni ingrandimenti supportati da un sistema automatico di analisi d’immagine. Il valore della durezza Vickers è un numero seguito dal simbolo HV e da un numero al pedice che indica il carico applicato al penetratore espresso in Kgf.
PROVA DI DUREZZA ROCKWELL (HR)
Il principio su cui si basa la durezza Rockwell, è differente da quello delle precedenti durezze richiedendo anche la valutazione della profondità di penetrazione (di alcuni µm), e richiede che il pezzo in prova sia perfettamente posizionato sul supporto del durometro. Tale situazione non esiste per le prove Brinell o Vickers nelle quali il penetratore lascia, alla fine, un’impronta di corrette dimensioni che è funzione della corsa del penetratore. Quest’ultimo è diverso in funzione del tipo di scala Rockwell definita, e può essere una sfera di metallo duro o un cono diamante che devono soddisfare i requisiti della norma UNI EN ISO 6508-2. Per evitare importanti errori nelle misurazioni, la norma UNI EN ISO 6508-1 fornisce diverse indicazioni sulla preparazione della provetta di prova, sulla sua planarità e grado di pulizia nonché sul suo spessore. Poiché le misure Rockwell con penetratore cono diamante, sono spesso usate per valutare la durezza di strati superficiali di pezzi cementati o temprati ad induzione, la norma UNI EN ISO 6508-1 indica quale scala HR usare in riferimento alla profondità dello strato. La lettura del valore di durezza Rockwell avviene, nel nostro laboratorio, direttamente sul quadrante digitalizzato dello strumento di misura. Le scale di durezza HR normate sono 15 ma le più usate e indicate nei disegni dei costruttori sono un numero inferiore.